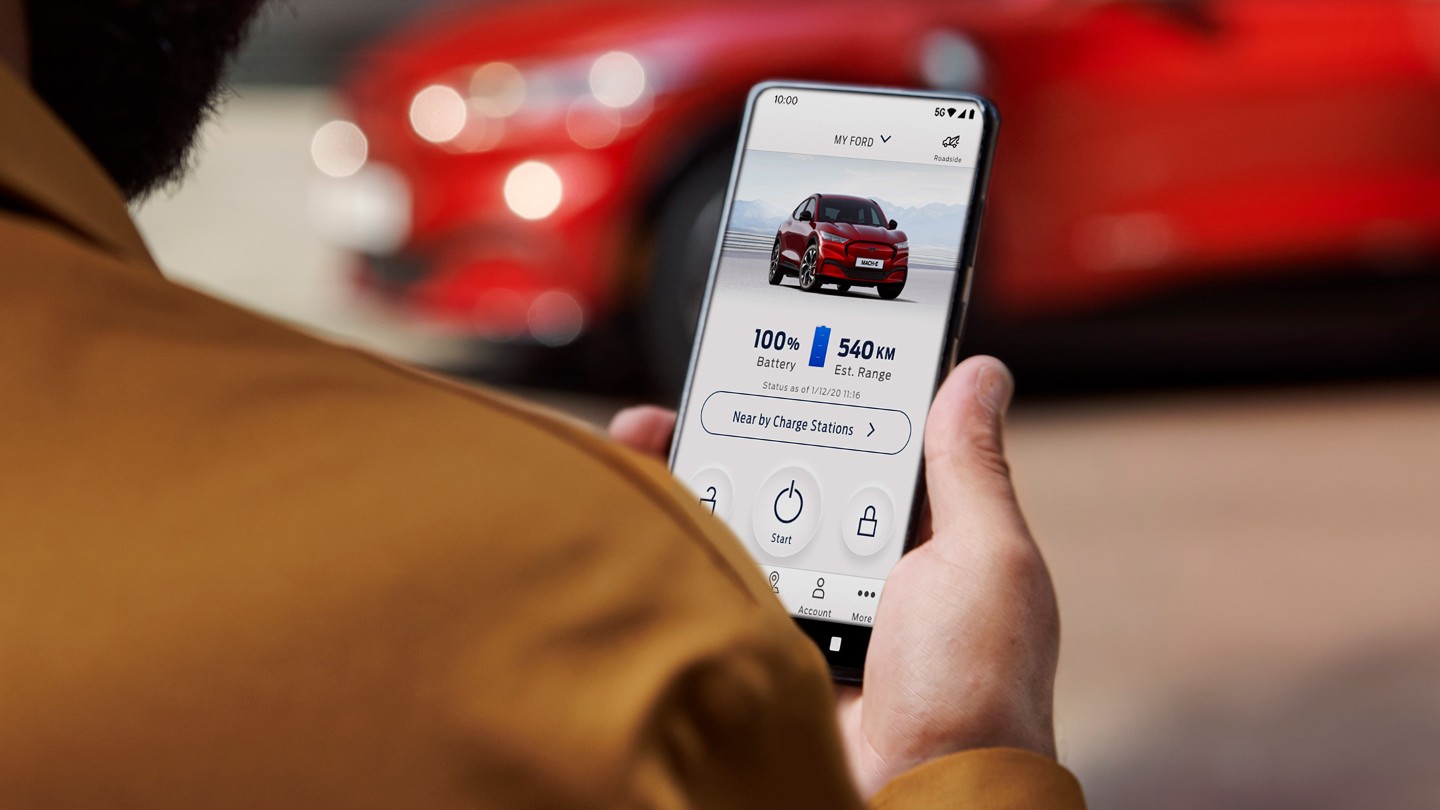
CONNECTIVITY
Discover seamlessly connected smart vehicles that keep you in touch, entertained and in control.
Every Ford we produce is packed with creativity and innovation. Technology that helps us build cleaner, quieter, more sustainable vehicles, and create smarter, safer, more connected driving experiences.